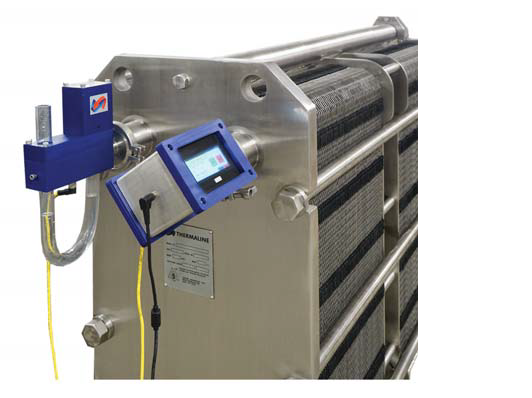
- Why Do You Need to Conduct Heat Exchanger Testing?
- How Often Should Heat Exchanger Testing Occur?
- Performing a Heat Exchanger Test
- Cross-Contamination Testing Explained
- The Testing Process
- Heat Exchanger Testing Models
- Thermaline Webinars
No matter the industry you’re in, heat exchangers are a key element of your overall heating or cooling process. As part of these complex processes, heat exchangers need to be able to perform at their optimal functionality, which is why regular heat exchanger testing is critical.
Whether you’re a Dairy processor, food processor, commercial brewery or in another industry, a lot of work goes into making your quality product ready for consumers. We understand these process challenges and are equipped to help you in every step of the process as you’re dealing with tightening regulations, high-speed production, and more.
Let’s explore why heat exchanger testing matters, what we test for at Thermaline, and how often we recommend testing.
Why You Need to Conduct Heat Exchanger Testing?
Heat exchangers can develop both internal or external defects. Take leaks, for instance. While external leaks are often more evident, as they are visible with fluid leaking to atmosphere, internal leaks are harder to detect and tend to develop gradually.
Internal leaks become problematic as they result in the mixing of two fluids, and contaminating your process. Since there’s less visibility into internal leaks – and even less predictability into when or how they may develop – it is crucial that frequent testing is performed on your heat exchangers. Other sources of cross-contamination can include weld failures, metal fatigue, stress corrosion, or mechanical wear. While external leaks may not contribute to contamination in your process, they still need to be addressed.
How Often Should Heat Exchanger Testing Occur?
Regulatory (and standards) recommendations by 3-A, the FDA, CFIA, and FSMA, point to doing heat exchanger testing at least once a year. Testing will include inspecting for things like internal defects, external defects, gasket inspection, cleanliness after CIP, correct plate installation and overall frame condition.
If you’re wondering if your equipment will need to be disassembled for the cross-contamination testing to occur, it’s not necessary. We also work to minimize any plant down-time through this type of testing. Our service department can also offer heat exchanger testing upon request. Use our certified testing providers, or schedule a CCT test.
There are definite benefits of testing in-house, including cost savings, quality assurance, and more regular testing but with minimizing exposure to outside visitors.
Performing a Heat Exchanger Test
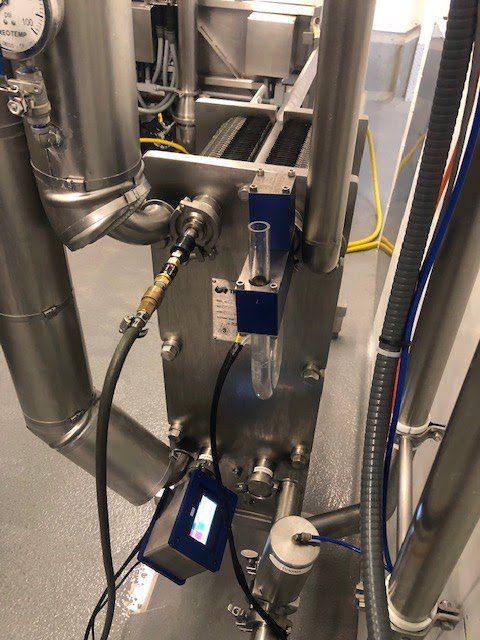
To safeguard against cross-contamination as a result of defects, we recommend a proactive testing approach and regular maintenance. Our Thermaline Cross Contamination Tester (CCT) program offers the most comprehensive and cost-effective testing to help identify problems, and address these as efficiently as possible.
Using our CCT, we can test your heat exchanger for any internal defects, and have answers within minutes. The CCT is easy to use and can be operated by your own trained plant personnel, and we believe it should be part of any processor’s overall food safety plan.
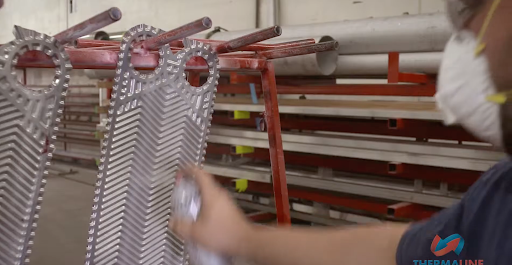
Without heat exchanger testing, it’s even harder to see what’s happening internally and detect a potential issue. Problems can emerge like high bacteria counts which can then lead to product recalls, product in your chiller or glycol in your product. Of course, you don’t want any of these things compromising the integrity of your product in any way, and face mounting costs as a result.
Cross-Contamination Testing Explained
We use our Thermaline CCT as a primary way to test an entire plate pack or tubular system for internal defects. If a heat exchanger passes this primary test, there’s no further need for additional testing. But, if a heat exchanger fails the primary test, we’ll do a secondary test to locate the defect (or pinpoint a leak).
Some companies use what’s known as “dye testing” as a primary test, but we’ve found this to be expensive (tens of thousands of dollars!), and time consuming. Not to mention, it’s hard for even a trained technician to perform this test with the attention required to read the results correctly.
The defects could cross-contaminate your product, and the CCT alerts us to any potential unseen issues. The CCT uses hydro-pneumatics to sense a defect, and inform you of the severity of the defect. This quick detection allows us to make an informed decision, and address the problem.
The Testing Process
Before we dive into testing methods, let’s start by dissecting what a heat exchanger consists of: two sides: which we’ll label A and B. On the “A” side of the heat exchanger, regulated plant air is introduced via a port. The PLC is attached on the opposite port of side A, and the CCT is connected to side B. The CCT allows us to perform an automatic visual test, and a calculated test.
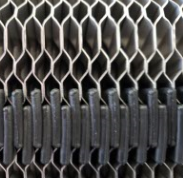
We’ll learn if a defect exists, if air passes through the defect from side A through to side B, which raises the atmospheric pressure of side B (resulting in bubbles in the tube and pressure change in the water column of the tube bubbler). We can assess the severity of the defect by using a correlation between time, volume, pressure and defect size.
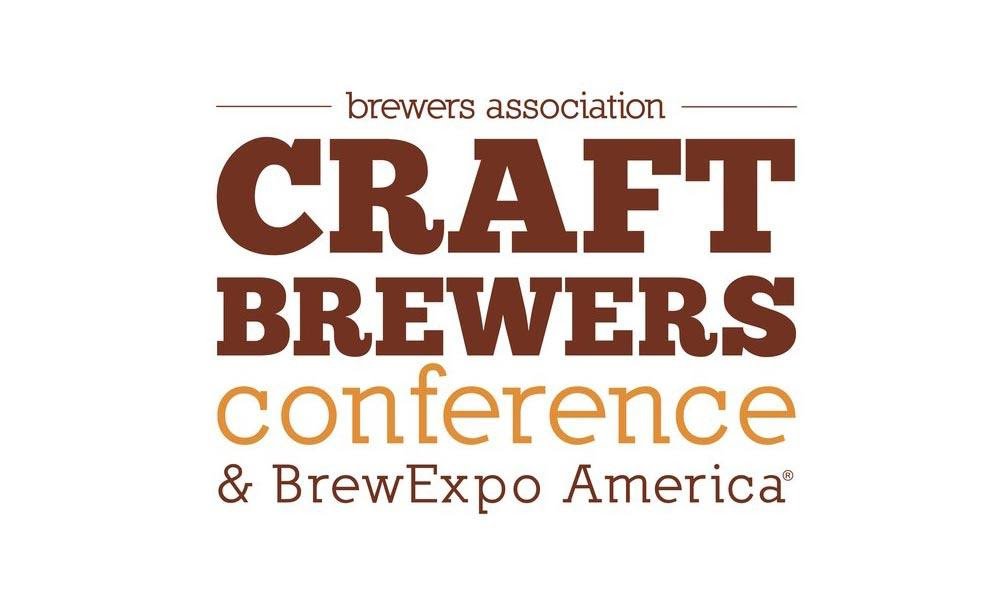
If you’re curious about how heat exchangers operate, or want to learn more about maintenance and testing, watch our informational videos!
Heat Exchanger Testing Models
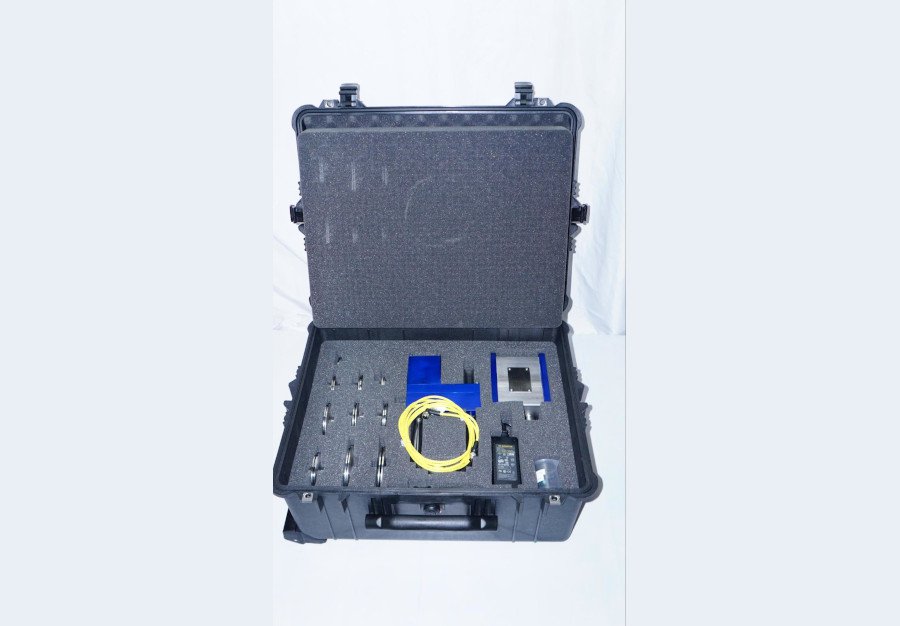
The Patented CCT 4.0 is a primary tester* which uses a PLC to calculate the volume of the heat exchanger.
It produces a PDF document report for your records. The CCT 4.0’s bubbler feature gives us a quick visual indication of internal defects. Constructed of stainless steel and aluminum, the rugged CCT 4.0 is built to last for years, and withstand rough environments. Our kit includes the following:- CCT 4.0 Primary Tester and pressure sensing PLC driver
- Power supply and interconnecting cable
- Air Pressure regulator and dump valve
- Heavy duty carrying case
- Spare connection O-rings
- Tri-Clamp connection kit 1", 1-1/2", 2", 2-1/2", and 3" (other connections available)
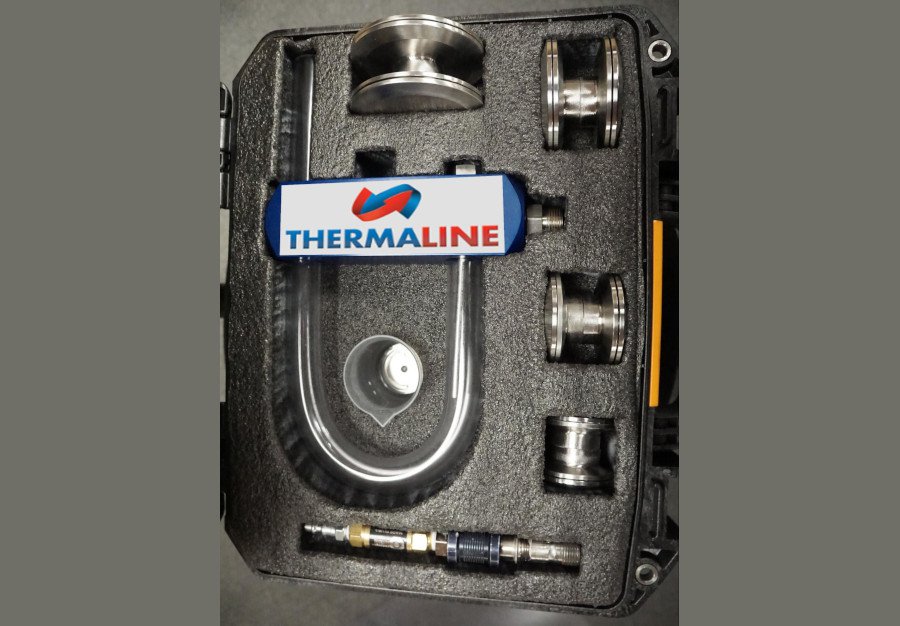
Our patented 2.0 is a primary tester* producing a pass or fail indication of internal defects regardless of heat exchanger size. The bubbler senses internal defects giving the operator visual results, and CCT 2.0 performs a timed duration test based on heat exchanger volume.
Our testing kit includes the following:- CCT 2.0 Primary Tester
- AirPressure regulator and dump valve
- Heavy duty carrying case
- Volume/Duration lookup chart
- Spare connection O rings
- Tri-Clamp Connection kit 1", 1-1/2", 2", 2-1/2", 3" (other connections available)
Thermaline Webinars
Our team understands process challenges associated with different industries, and can design the right, dependable heat exchanger around your process requirements. We offer a wide range of plate, shell and tube, and corrugated tube heat exchangers to fit your specific needs. Check out our recorded webinars for a deeper look into different aspects of the industry!