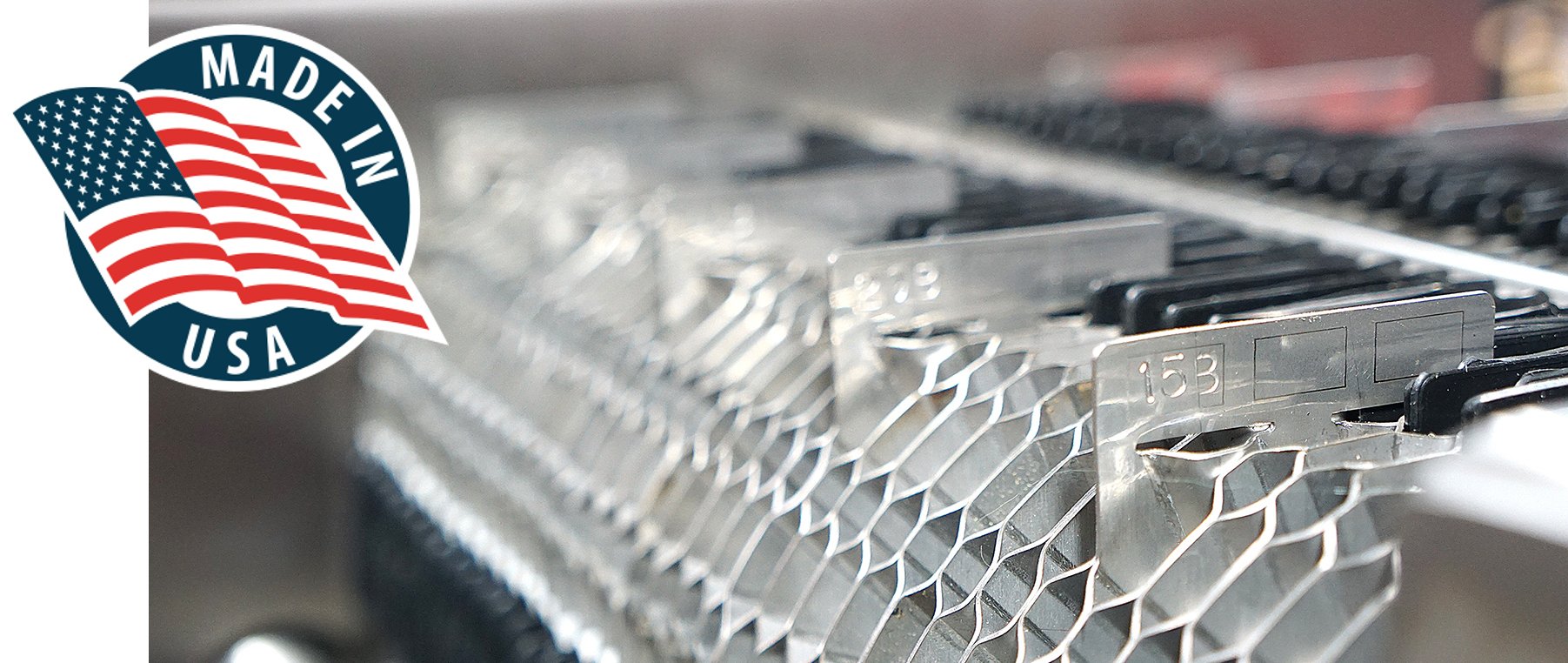
- Heat Exchanger Design Parameter: Fluid Product Type
- Understanding Heat Exchanger Types: Plate and Frame Heat Exchangers
- Corrugated Tubular Heat Exchangers
- Shell and Tube Heat Exchangers
- Selection Guidelines for Your Heat Exchanger
- Stay up to date with Team Thermaline
Before we dive into explaining heat exchanger types, including plates vs. tubular heat exchangers, we want to take a step back and explain their functionality.
Heat exchangers allow for the transfer of heat between two or more fluids (which can either be mixed or be in direct contact). They can be used in cooling, and heating, processes including refrigeration, air conditioning, space heating, natural-gas processing, and more.
A few key parameters that determine heat exchanger design include:
- fluid product type
- process requirements
- thermal efficiency
- floor space availability
- regulations
- future expandability
- food grade design
- industrial design and ASME Code Stamps
We’ll focus on product type as the main parameter.
Heat Exchanger Design Parameter: Fluid Product Type
Our heat exchanger design is informed by fluid product types. Let’s go a little further and talk about fluid product types, and how these can be broken down into 4 main categories.
- Water-like fluids with no particulates have characteristically low viscosity, and include fluids like milk, juices, or other beverages.
- Water-like fluids with particulates with a low-to-medium viscosity include pulpy juices, purees, or slurries.
- Thicker fluids with no particulates with a medium-to-higher viscosity include fluids such as syrups, concentrates, and creams.
- Thicker fluids with particulates with a higher viscosity include sauces, salsas, and soups.
Understanding Heat Exchanger Types: Plate and Frame Heat Exchangers
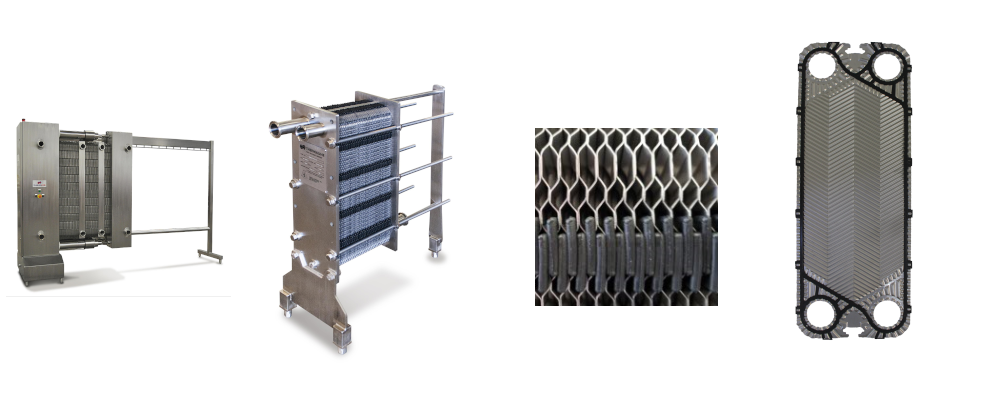
Working towards balancing between energy efficiency, optimal performance, and dependability is a complicated equation but Thermaline’s years of industry experience and team can assist and navigate through your process needs. Our sanitary plate heat exchangers can be used across processing for dairy, juice, condiments, wine and beer products.
Their stainless steel frame is highly polished for complete cleanability (and solid heads safeguard against bacteria), and their rugged design lasts for years of service. In addition to cleanability, they feature leak detection and sanitization portals. These exchangers have multiple mounting options, and customizable connections that allow for adapting to new processes. Sanitary carbon steel frames have rugged, high-temperature powder coating, a stainless steel tie bolt, and sanitary wetted surfaces and customizable connections.
When we think about heat exchangers in relation to fluid product types, plate and frame heat exchangers are especially great for thin-liquid products with no particles. These heat exchangers consist of a series of corrugated thin metal plates, which are pressed together in a frame and are sealed by a gasket. They can have a manual or automated closing feature. (maybe include a video for further explanation) Overall, plate and frame heat exchangers are highly energy efficient, compact (space efficient), and come at the lowest cost for exchange surfaces. Sanitary 3A food grade is standard.
Thermaline’s mix proof double wall plates prevent cross-contamination of your low viscosity fluids. Two plates are paired together to form one plate with a safety micro air gap in between the plates. If either of the plates fail from corrosion or cracks, the process fluids will not mix. Instead, the fluid against the failed plate will be directed through the micro air gap and to the outside of the heat exchanger, where it becomes visible. These heat exchangers can be applied in Pharmaceutical, Bio-Tech, Personal Care, Potable Water, Food, Bio Pharma, Beverage Processing.
As an added step, Thermaline’s patent-pending Smart Identification System (SIS) was designed to ensure your plate heat exchanger is assembled properly. Even the most hygienic designs cannot safeguard against human error, and one wrong move can cost more than a financial burden: it can lead to a recall destroying your brand. Using our SIS, we’re able to laser etch vital plate information on external tabs that is visible at a glance, even when the unit is assembled.
Corrugated Tubular Heat Exchangers

The innovative design of our tubular heat exchangers allows the tubes to freely expand and contract independently which diminishes material fatigue and failure. Thermaline’s Floating Series completely eliminates failure-prone expansion bellows and rigid welds on all models. The product flow and heating/cooling media flow are separated in concentric lengths of sanitary tubing. The unit has no moving parts, is easy to clean, easy to inspect, and easy to maintain. Tube ends, with their sanitary clamp design, can be easily removed for QC inspections and maintenance.
The strategically-positioned elastomers eliminate the possibility of product intermixing. If a leak were to develop from an elastomer failure, the fluid would be vented to the atmosphere so it can be quickly identified and repaired. The Floating Series eliminates blind, internally-positioned elastomers that can lead to cross contamination.
The heat exchanger surface is shaped into turbulence-inducing, alternating parallel grooves and ridges to increase heat transfer efficiency. Inducing turbulent flow results in less total surface area required to achieve the desired thermal results. Turbulent flow promotes thorough mixing of the product and even thermal disbursement without compromising product integrity.
Tubes can easily be arranged in either direct, or indirect, regeneration. Direct product regeneration can yield more than 80% in energy savings. Indirect product regeneration can recover energy from thermal waste streams in other areas of your facility, reducing thermal pollution and increasing energy savings.
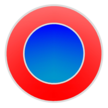
Double tube “DuoFloat” heat exchangers (a tube inside of a tube) consist of a center tube for product, and an outer tube for service media. Adding the Duofloat inline mixer to your double-tube heat exchanger enables you to tune your processing needs to a variety of products. When processing fluids with large particulates, remove the DuoFloat inline mixer to maintain product integrity and then easily reinstall the mixers to ensure thorough heat transfer on your other viscous products.
These types of heat exchangers are great for products with large particles suspended in liquid. The heat exchanger consists of two concentric corrugated tubes one inside the other, with each end sealed by an O-ring. Corrugation adds to thermal transfer efficiency. All parts are removable for inspection or replacements, and standard lengths are 10’, 20’ and 30’. Sanitary 3A food grade is standard.
Triple Tubes:

Triple Tube heat exchangers “TriFloat” (tube inside of tube, inside of tube) consist of an intermediate tube for product, a center tube, and a jacket tube for service. They are capable of passing medium particles suspended in fluid, and corrugations add to thermal transfer efficiency. All parts are removable for inspection or replacements, with standard lengths being 10’, 20’ and 30’. Sanitary 3A food grade is standard for triple tube heat exchangers.
Multi Tubes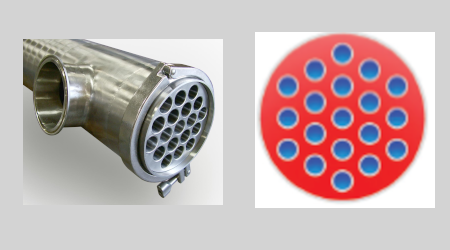
Multi-Tube heat exchangers (“MultiFloat”) consist of a group of small tubes for a product inside a single larger tube for service media. These types of heat exchangers are capable of passing small-to-medium particles suspended in fluid, and each end is sealed by O-rings and gaskets. Corrugation adds to thermal transfer efficiency. All parts are removable for replacements, and inspection, with standard lengths of 10’, 20’ and 30’. Sanitary 3A food grade is standard.
When product integrity is an absolute necessity, Thermaline offers a sanitary corrugated floating multi-tube heat exchanger with additional safety features. The product tube face is separated from the media tube face, eliminating the possibility of product cross contamination from tube-to-tube sheet failures.
Shell and Tube Heat Exchangers
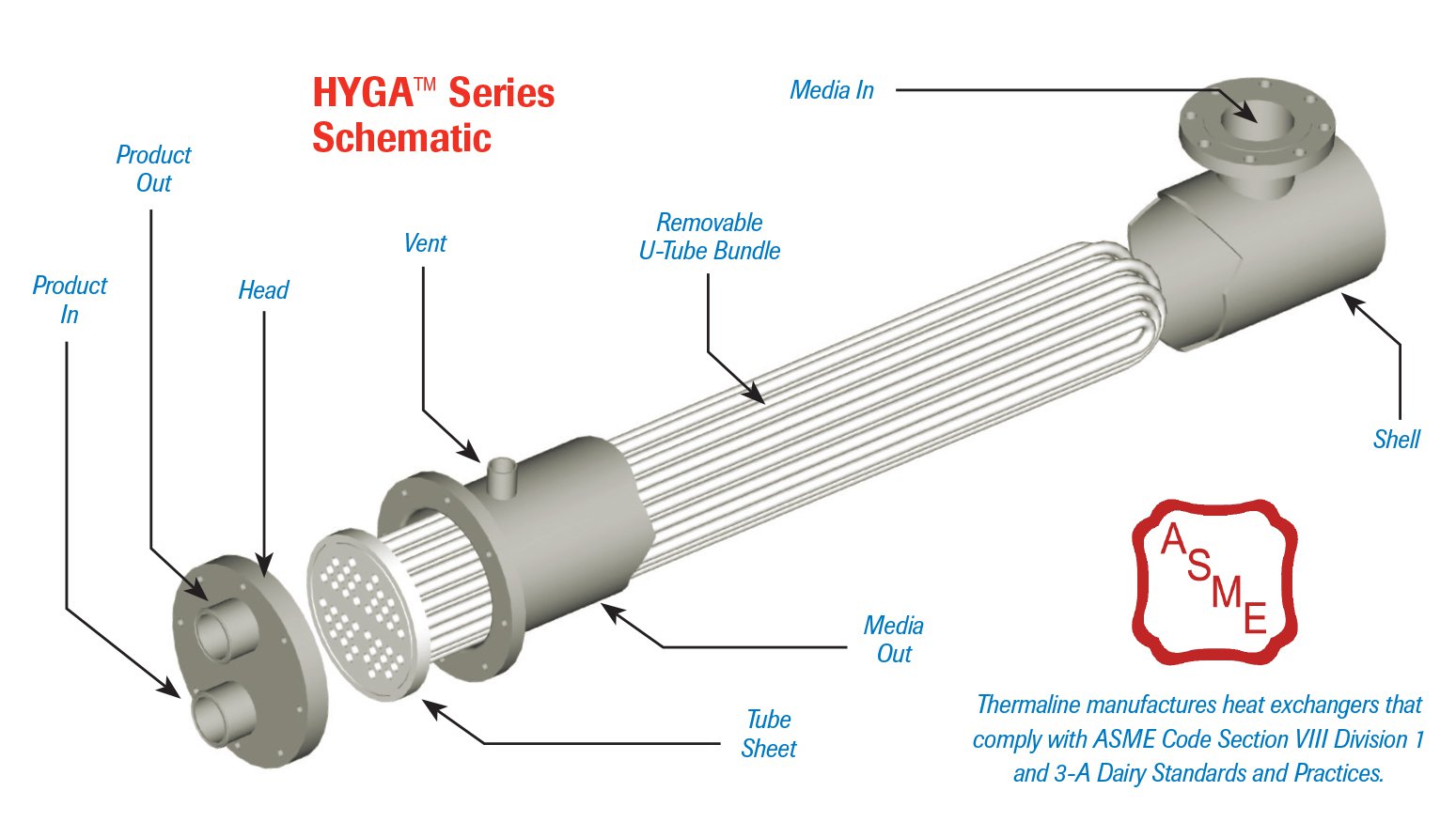
Thermaline stainless steel Shell & Tube heat exchangers are manufactured in accordance with ASME and TEMA standards. They come standard with a mechanical solid seal backed with a self energized o-ring ensuring years of uninterrupted service.
Shell and tube heat exchangers are ideal for thin fluids with little-to-no particulates. They consist of a U-bend tube bundle to allow for multiple passes in the same shell. These heat exchangers are ideal for steam, and condensing, processes, and are available for Utility, Food and Bio-pharma processes.
Selection Guidelines for Your Heat Exchanger
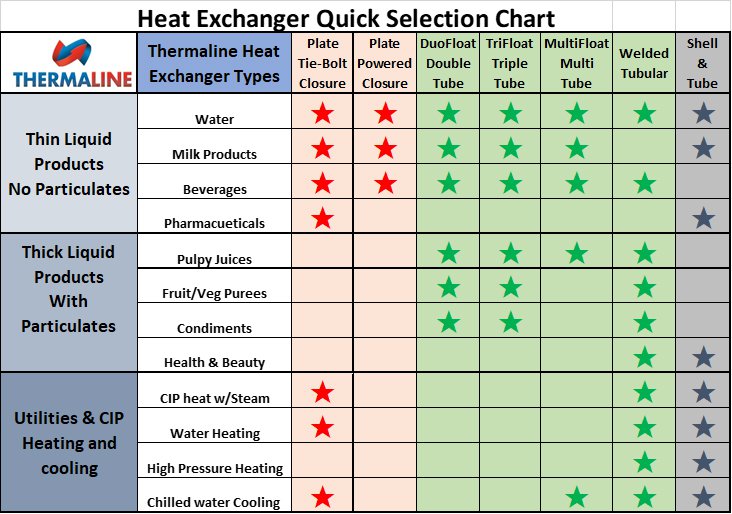
In order to best meet your process needs, our team follows selection guidelines depending on the product type category. Based on design parameters, we’ll be able to determine the type of heat exchanger that matches the product type. A Thermaline applications engineer will consult with you to help you choose the optimum heat exchanger for your process.
In addition to matching up the type of fluid product with a heat exchanger type, we take into account additional parameters required to accurately design, and quote, heat exchangers.
These design parameters include:
- The product fluid(s) name(s) and physical properties (specific gravity, thermal conductivity, viscosity, brix and solids %), if available.
- Service Media name, and physical properties, if other than water.
- Expected process flow rate(s)
- Desired temperatures for the product inlet and outlet.
- Maximum allowable pressure drops across the heat exchanger.
- Desired future expansion plans, if known.